Research result 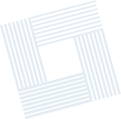
해외논문
-
Enhanced Microstructure and Wear Resistance of Ti–6Al–4V Alloy with Vanadium Carbide Coating via Directed Energy Deposition
Ti–6Al–4V alloys are known for their suboptimal tribological properties and are often challenged by durability issues under severe wear conditions. This study was conducted to enhance the alloy’s wear resistance by forming a hardened surface layer. Utilizing directed energy deposition (DED) additive manufacturing with a diode laser, vanadium carbide particles were successfully integrated onto a Ti–6Al–4V substrate. This approach deviates from traditional surface enhancement techniques like surface hardening and cladding, as it employs DED additive manufacturing under parameters akin to those used in standard Ti–6Al–4V production. The formed vanadium carbide layer achieved a remarkable thickness of over 400 µm and a Vickers hardness surpassing 1500 HV. Pin-on-disk test results further corroborated the enhanced surface wear properties of the Ti–6Al–4V alloy following the additive-manufacturing process. These findings suggest that employing vanadium carbide additive manufacturing, under conditions similar to the conventional DED process with a diode laser, significantly improves the surface wear properties of Ti–6Al–4V in metal 3D-printing applications.
2024-07-09 13:32
-
A Study on the Effect of Shape and Number of Supports in Additive Manufacturing Process by Using a Macro Heat Transfer Analysis
The development of robust and efficient methods for constructing and joining complex metal specimens with high bonding quality and durability is of paramount importance for various industries, e.g., aerospace, deep space, and automobiles. This study investigated the fabrication and characterization of two types of multilayered specimens prepared by tungsten inert gas (TIG) welding: Ti–6Al–4V/V/Cu/Monel400/17-4PH (Specimen 1) and Ti–6Al–4V/Nb/Ni–Ti/Ni–Cr/17-4PH (Specimen 2). The specimens were fabricated by depositing individual layers of each material onto a Ti–6Al–4V base plate, and subsequently welding them to the 17-4PH steel. The specimens exhibited an effective internal bonding without any cracks, accompanied by a high tensile strength, with Specimen 1 exhibiting a significantly higher tensile strength than Specimen 2. However, the substantial interlayer penetration of Fe and Ni in the Cu and Monel layers of Specimen 1 and the diffusion of Ti along the Nb and Ni–Ti layers in Specimen 2 resulted in a nonuniform elemental distribution, raising concerns about the lamination quality. This study successfully achieved elemental separation of Fe/Ti and V/Fe, which is vital for preventing the formation of detrimental intermetallic compounds, particularly in the fabrication of complex multilayered specimens, representing the prime novelty of this work. Our study highlights the potential of TIG welding for the fabrication of complex specimens with high bonding quality and durability.
2024-07-09 13:31
-
Interlayer Tailoring of Ti–6Al–4V and 17-4PH Stainless Steel Joint by Tungsten Inert Gas Welding
The development of robust and efficient methods for constructing and joining complex metal specimens with high bonding quality and durability is of paramount importance for various industries, e.g., aerospace, deep space, and automobiles. This study investigated the fabrication and characterization of two types of multilayered specimens prepared by tungsten inert gas (TIG) welding: Ti–6Al–4V/V/Cu/Monel400/17-4PH (Specimen 1) and Ti–6Al–4V/Nb/Ni–Ti/Ni–Cr/17-4PH (Specimen 2). The specimens were fabricated by depositing individual layers of each material onto a Ti–6Al–4V base plate, and subsequently welding them to the 17-4PH steel. The specimens exhibited an effective internal bonding without any cracks, accompanied by a high tensile strength, with Specimen 1 exhibiting a significantly higher tensile strength than Specimen 2. However, the substantial interlayer penetration of Fe and Ni in the Cu and Monel layers of Specimen 1 and the diffusion of Ti along the Nb and Ni–Ti layers in Specimen 2 resulted in a nonuniform elemental distribution, raising concerns about the lamination quality. This study successfully achieved elemental separation of Fe/Ti and V/Fe, which is vital for preventing the formation of detrimental intermetallic compounds, particularly in the fabrication of complex multilayered specimens, representing the prime novelty of this work. Our study highlights the potential of TIG welding for the fabrication of complex specimens with high bonding quality and durability.
2024-07-09 13:30
-
Homogenization on solution treatment and its effects on the precipitation-hardening of selective laser melted 17-4PH stainless steel
17-4 precipitation-hardened (PH) stainless steel (SS) exhibits high strength and good corrosion resistance via Cu-precipitation hardening. Unlike conventional wrought 17-4PH SS, Cu segregation and ε-Cu precipitates are observed in additively manufactured (AM) 17-4PH SS owing to the repeated rapid cooling after heating, which characterizes the AM process. In this study, solution treatment was conducted under various temperatures (1,000, 1,050, 1,100, and 1,200 °C) and durations (1, 2, 4, and 8 h) to minimize the negative effects of Cu segregation and ε-Cu precipitates on precipitation hardening. The mechanical properties and microstructures of each condition for the Cu precipitation behavior were examined. Although the ε-Cu precipitates did not disappear after solution treatment, the average diameter of the ε-Cu precipitates tended to decrease with increasing solution treatment temperature and duration. Therefore, solution treatment at a temperature of 1,200 °C for 8 h was the best, resulting in improved strength compared to the conventional solution treatment at 1,050 °C. Solution treatment on at least 1,100 °C is effective in AM.
2024-07-09 11:26
-
Influence of Heat Treatment on the Microstructure and Hardness of 17-4PH Stainless Steel Fabricated Through Direct Energy Deposition
AISI 630 stainless steel (ASTM A564-89, 17-4PH) is widely used in die-casting molds owing to its excellent wear and heat resistance. Recently, a cooling strengthening technology that densifies the microstructure of the casting through rapid cooling has been developed. Additive manufacturing can be used to fabricate casting molds with complex three-dimensional cooling channels. 17-4PH stainless steel, a martensitic precipitation hardening steel, can be subjected to heat treatment to improve its mechanical properties, which are highly dependent on its microstructure. Specifically, the formation of martensite and δ-ferrite, and the coarsening of Cu-rich precipitates considerably decreases the hardness of 17-4PH stainless steel. In this study, we investigate the microstructural evolution of 17-4PH stainless steel during aging and solution heat treatment processes and determine their effect on the formation of martensite and δ-ferrite. Furthermore, the effect of heat treatment on the microstructure and hardness of the steel is studied experimentally. Accordingly, three specimens—as-built, H-1150-M (aging heat treatment), and SH-1150-M (solution and aging heat treatment)—were analyzed and compared herein. The results revealed that the martensite fraction was the highest in the aged H-1150-M specimen, resulting in a high hardness. In contrast, in the SH-1150-M specimen, the austenite and δ-ferrite fractions were higher than the martensite fraction, resulting in a lower hardness than those of the other two specimens. Therefore, aging heat treatment without solution heat treatment can effectively increase the hardness of additively manufactured 17-4PH stainless steel.
2024-07-09 11:21
-
The design and additive manufacturing of an eco-friendly mold utilized for high productivity based on conformal cooling optimization
This study proposes an eco-friendly (ECO) mold that is fabricated using the laser powder bed fusion (LPBF) method, which utilizes a three-dimensional (3D) cooling channel. Unlike previous studies, we designed surface-type conformal cooling channels (CCC) based on the design concept for additive manufacturing, at a constant depth corresponding to the casting part. Pin fins were installed inside the surface-type cooling channels and aligned through numerical analysis to induce the turbulence of the coolant uniformly through the cooling channel while generating less thermal stress during solidification of the as-cast Al-Si alloy-based product, which increased the cooling efficiency of the proposed ECO mold. Moreover, the ECO mold was utilized to cast an automobile piston to demonstrate its feasibility at an industrial level. The results showed that, the casting process decreased significantly from 133 to 105 s per piston (21% reduction) compared to the conventional mold with a single columnar cooling channel. Additionally, the average grain size of the ECO mold decreased from 502 to 398 µm. The ultimate tensile strength and Rockwell hardness increased by 12.5% and 5.5%, respectively.
2024-07-09 11:17
-
Normalizing effect of heat treatment processing on 17-4 PH stainless steel manufactured by powder bed fusion
Laser powder bed fusion (L-PBF)-processed 17-4 PH stainless steel (SS) generally exhibits a non-equilibrium microstructure consisting mostly of columnar δ-ferrite grains and a substantial fraction of retained austenite and martensite, contrary to 17-4 PH SS wrought with a fully martensite structure and coarse grains. Despite the different microstructures of L-PBF and wrought 17-4 PH SS, post-processing is typically performed using the conventional heat treatment method. The insufficient effect of the heat treatment on the L-PBF product produces a δ-ferrite phase in the microstructure. To obtain improved mechanical properties, the addition of a normalizing treatment to the conventional heat treatment after L-PBF in a nitrogen gas environment was investigated. The fully martensitic matrix developed by adding the normalizing treatment contained homogeneous Cu precipitates and exhibited a similar or improved strength and elongation to failure compared to the wrought SS.
2024-07-09 11:12
-
Tensile test of additively manufactured specimens with external notch removed via laser cutting in material extrusion
• Tensile test considering the external notch of the materials extrusion specimens. • Remove notches using laser cutting. • Minimize heat affected zone (HAZ) by establishing laser cutting conditions. • Increased fracture within gauge length in tensile load via remove notch.
2024-07-09 11:11
-
Understanding the Mechanism of Magnesiothermic Reduction for Direct Alloy Synthesis of Ti-Nb Alloys
A novel approach to directly produce Ti-Nb alloys through direct magnesiothermic reduction from intermediate TiNb2O7 (TNO) is demonstrated. Using a combination of X-ray diffraction, scanning electron microscope–energy dispersive spectroscopy, and scanning transmission electron microscopy, the observed phases, chemical composition, and crystal structure could be identified and the reaction pathway determined. Although thermodynamically favorable, the reductions carried out between 700°C and 900°C at various Mg/TNO stoichiometric molar concentrations showed 1.5 times the stoichiometric molar ratio (mass ratio Mg/TNO of 10.5) to produce Ti-Nb alloy products, but complete reduction was not possible owing to the depletion of Mg from vaporization and reactions. Excess amounts of Mg at 5 times the stoichiometric molar ratio (mass ratio Mg/TNO of 35) resulted in full reduction of the TNO powders to produce Ti-Nb alloys without Ti-Nb-Mg-O intermediate oxide phases. A comparison of the magnesiothermic reduction of the individual components, including TiO2, Nb2O5, and TNO, indicated the reduction of TiO2 to be complex and limiting, with reduction significantly easier for Nb2O5 and TNO at higher temperatures and excess Mg contents.
2024-07-03 21:02
-
Magnesiothermic reduction for direct synthesis of Ti-Nb alloy at 1073 K (800℃)
Direct fabrication of titanium (Ti) and niobium (Nb) alloys by direct magnesiothermic reduction from the respective initial metal oxides and complex oxides has been studied. TiO2, Nb2O5, and complex TiNb2O7 oxides were used as raw materials with Mg used as a reductant. To ensure a high chemical potential of the reactants to drive the spontaneous magnesiothermic reduction of the oxide mixtures, excess Mg five times higher than the required stoichiometric molar ratio was added. Samples were heated in a glove box under recycled and purified Ar atmosphere at 1073 K (800 °C) for 10 h. After the reduction of TiO2, intermediate oxide phases of Ti6O could still be observed, but reduction of Nb2O5 and TiNb2O7 showed metallic Nb and Ti-Nb to be present with negligible oxides according to the scanning electron microscope-energy dispersive spectroscopy and x ray diffraction analysis. This indicated that direct fabrication of Ti-Nb alloys through a complex TiNb2O7 oxide is possible and can be more efficient than alloying pure metallic elements of Ti and Nb.
2024-07-03 21:00
-
Reaction Kinetics and Morphological Study of TiNb2O7 Synthesized by Solid-State Reaction
Although TiNb2O7 is regarded as a material with high application potential in lithium-ion batteries (LIBs) and solid-oxide fuel cells (SOFCs), it has been difficult to find suitable cost-effective conditions for synthesizing it on a commercial scale. In this study, TiNb2O7 compounds were synthesized by a solid state synthesis process. For stoichiometrically precise synthesis of the TiNb2O7 phase, the starting materials, TiO2 and Nb2O5 were taken in a 1:1 molar ratio. Activation energy and reaction kinetics of the system were investigated at various synthesis temperatures (800,1000,1200, and 1400°C) and for various holding durations (1,5,10, and 20 h). Furthermore, change in the product morphology and particle size distribution were also evaluated as a function of synthesis temperature and duration. Additionally, quantitative phase analysis was conducted using the Rietveld refinement method. It was found that increases in the synthesis temperature and holding time lead to increase in the mean particle size from 1 to 4.5 µm. The reaction rate constant for the synthesis reaction was also calculated.
2024-07-03 20:58
-
Understanding the Magnesiothermic Reduction Mechanism of TiO2 to Produce Ti
Titanium dioxide (TiO2) powders in the mineral form of rutile were reduced to metallic and an intermediate phase via a magnesiothermic reaction in molten Mg at temperatures between 973 K and 1173 K (700 °C and 900 °C) under high-purity Ar atmosphere. The reaction behavior and pathway indicated intermediate phase formation during the magnesiothermic reduction of TiO2 using XRD (X-ray diffraction), SEM (scanning electron microscope), and TEM (transmission electron microscope). Mg/TiO2 = 2 resulted in various intermediate phases of oxygen containing titanium, including Ti6O, Ti3O, and Ti2O, with metallic Ti present. MgTi2O4 ternary intermediate phases could also be observed, but they were dependent on the excess Mg present in the sample. Nevertheless, even with excessive amounts of Mg at Mg/TiO2 = 10, complete reduction to metallic Ti could not be obtained and some Ti6O intermediate phases were present. Although thermodynamics do not predict the formation of the MgTi2O4 spinel phase, detailed phase identification through XRD, SEM, and TEM showed significant amounts of this intermediate ternary phase even at excess Mg additions. Considering the stepwise reduction of TiO2 by Mg and the pronounced amounts of MgTi2O4 phase observed, the rate-limiting reaction is likely the reduction of MgTi2O4 to the TitO phase. Thus, an additional reduction step beyond thermodynamic predictions was developed.
2024-07-03 20:51
-
Effect of magnesium on the phase equilibria in magnesio-thermic reduction of Nb2O5
• Molar fraction of Mg influences the magnesio-thermic reduction kinetics of Nb2O5. • Intermediate Mg-Nb-O oxides can form depending on the Mg content. • Higher temperatures enhanced formation kinetics of intermediate Mg-Nb-O oxides. • Fully reduced metallic Nb was immiscible with the surrounding MgO. • FCC Mg-Nb-O and hexagonal Mg3Nb6O11 phases were identified.
2024-07-03 20:48
-
Effect of Rb2O and Cs2O on Inclusion Removal in 321 Stainless Steels Using Novel Basic Tundish Fluxes
Inclusion removal and modification of the 321 stainless steel using Rb2O- and Cs2O-containing novel basic tundish flux has been investigated. The average inclusion diameter was significantly lowered after reaction of the liquid metal with the flux after 45 minutes in an induction furnace set at 1823 K (1550 °C) under an Ar atmosphere. The number of inclusions was also decreased with increased reaction time and the majority of the inherent TiN inclusions were removed after reaction with the proposed novel basic tundish flux. Spinel inclusions were also observed after the reaction, which was due to the reaction of the MgO crucible and the CaO-Al2O3-SiO2-MgO-‘x’wt pct R2O flux system at fixed CaO/(Al2O3 + SiO2) of 1.45. The Rb2O and Cs2O seemed to have allowed significant removal of the TiN inclusions due to its ion compensation effect and the supplement of free oxygen ions, while increasing the viscosity of the slag to retain the absorbed inclusions.
2024-07-03 20:46
-
Achieving a Carbon Neutral Society without Industry Contraction in the Five Major Steel Producing Countries
This study analyzed the direct and indirect CO2 emissions of the energy-intensive basic metals industry, in particular steels, using the distributions of various energy sources, including coal/peat, oil, and electricity, from an input–output table. An analysis of five major steel producing countries indicated that direct CO2 emissions increased 1.4-fold and that indirect CO2 emissions increased by more than two-fold between 1995 and 2010. The elasticity of the CO2 emissions and the total energy costs indicated that Korea, Japan, and Germany are sensitive to energy sources from the electric power industry, whereas China and the US are more sensitive to energy sources pertaining to the coal and oil industry. Using the available forest area and photosynthesis, the potential neutralization ability of CO2 was estimated using the eco-CO2 index. The US yielded the highest CO2 neutralization ability of 66.1%, whereas Korea yielded a CO2 neutralization ability of 15%. Future trends of the 2030 eco-CO2 index revealed China and Korea will rapidly lose their neutralization ability resulting in a net negative neutralization ability if left unabated. The significant decline in the eco-CO2 index for the basic metals industry may be inhibited by utilizing bamboo wood charcoal for pulverized coal injection (PCI) in the steelmaking process.
2024-07-03 20:43
-
Enhancement of Ru nucleation in Ru-metal organic chemical vapor deposition by electron cyclotron resonance plasma pretreatment
For the deposition of Ru on TiN films by metal-organic chemical vapor deposition, pretreatment of the TiN film surface with Electron Cyclotron Resonance (ECR) plasma is essential to enhance Ru nucleation. In the present work, the effects of hydrogen, argon and oxygen plasma treatments on Ru nucleation, induced by Metal-Organic Chemical Vapor Deposition (MOCVD), were investigated using scanning electron microscopy, Auger electron emission spectroscopy and X-ray diffraction analyses. Ru nucleation is enhanced with increasing hydrogen or argon ECR plasma exposure time, while it decreases with increasing oxygen ECR plasma exposure time. Hydrogen ions in the hydrogen plasma react with TiN to form Ti and NH3. Argon ions in the argon plasma remove nitrogen or oxygen atoms from the top surface of the TiN or TiON film during the argon plasma treatment. The highest Ru nucleation density was obtained on TiN when the underlying TiN surface is pretreated with argon ECR plasma.
2024-07-03 20:37
-
Comparison of the removal efficiency for organic contaminants on silicon wafers stored in plastic boxes between UV/O3 and ECR oxygen plasma cleaning methods
When wafers are stored in a plastic storage box to protect them from airborne contaminants, volatile organics from the polymeric construction material adsorb onto the wafer surface. Both UV/O3 and ECR oxygen plasma techniques have been found to completely remove these organic contaminants adsorbed on the silicon surfaces up to the detection limit. After cleaning, Si wafers were characterized using attenuated total reflection-Fourier transform infrared spectroscopy (ATR-FTIR) and atomic force microscopy (AFM). Organic contaminants were eliminated more efficiently by the ECR oxygen plasma technique than the UV/O3 technique when they were employed under optimum process conditions.
2024-07-03 20:33
-
Removal efficiency of organic contaminants on Si wafer by dry cleaning using UV/O3 and ECR plasma
The removal efficiency of the organic contaminants existing on the surface of silicon wafers by a dry cleaning method using UV/O3 and ECR plasma is discussed in this paper. After cleaning, Si wafers are characterized by attenuated total reflection-Fourier transform infrared spectroscopy (ATR-FTIR) and atomic force microscropy (AFM). In UV/O3 cleaning, the exposure time to reach the detection limit for organic contaminants in ATR-FTIR is about 10 min and the RMS surface roughness reduces with increasing exposure time. In ECR hydrogen plasma cleaning, the RMS surface roughness reduces significantly with increasing the exposure time but the removal of organic contaminants from the silicon wafer is not very effective. In ECR oxygen plasma cleaning, the exposure times to reach both the detection limit and the lowest RMS roughness are 40 and 10 s, respectively, and the optimum exposure time is suggested to be 30–40 s, considering both the effects of cleaning and surface roughening. Therefore, dry cleaning using ECR oxygen plasma seems to be more effective than that using ECR hydrogen plasma or the UV/O3 cleaning for the removal of organic contaminants. Also, the removal mechanisms of the organic contaminants in UV/O3 and ECR plasma cleanings are discussed in detail.
2024-07-03 20:32
-
Semiconductors-Enhancement of Ru Nucleation in Ru-Metal Organic Chemical Vapor Deposition by Electron Cyclotron Resonance Plasma Pretreatment
2024-07-03 20:30
-
Removal efficiency of organic contaminants using ECR H2 plasma and ECR O2 plasma
In this communication, we report our experimental results on the removal of the organic contaminants existing on the surface of silicon wafers by a dry cleaning method using ECR plasma. After cleaning, Si wafers were characterized by Attenuated Total Reflection-Fourier Transform Infrared Spectroscopy (ATR-FRIR) and Atomic Force Microscopy (AFM). In ECR hydrogen plasma cleaning, the RMS surface roughness reduced significantly with increasing the exposure time but the removal of organic contaminants from the silicon wafer was not very effective. In ECR oxygen plasma cleaning, the plasma exposure times to reach both the detection limit and the lowest RMS roughness were 40 and 10 sec, respectively and the optimum plasma exposure time is suggested to be 30 {approx} 40 sec, considering both the effects of cleaning and surface roughening. Therefore, dry cleaning using ECR oxygen plasma seems to be more effective than that using ECR hydrogen plasma for the removal of organic contaminants.
2024-07-03 20:28
-
Effects of deposition parameters on the properties of chromium carbide coatings deposited onto steel by sputtering
Chromium carbide films were deposited on high speed steels using a Cr3C2 target by magnetron sputtering. Effects of the deposition parameters (power, Ar pressure and substrate temperature) on deposition rates and surface roughnesses of the films were investigated. The crystal structures and morphologies of those films were characterized by X-ray diffraction, scanning electron microscopy and atomic force microscopy. The as-deposited Cr3C2 films of most of the samples are amorphous in nature. The grain size of the samples deposited using dc-power is larger than that using equivalent rf-power. The hardness of the sample increases with increasing rf-power, whereas the elastic modulus nearly does not change with rf-power. The optimum sputter deposition conditions for Cr3C2 on high speed steels in the corrosion resistance aspect were found to be the dc-power of 200 W, the pressure of 7 mTorr and room temperature.
2024-07-03 20:26
-
Cu CONTAMINANT REMOVAL USING UV/O3 AND REMOTE HYDROGEN PLASMA
Removal of Cu contaminants from Si wafer was carried out using remote hydrogen plasma (RHP) and UV/O3 cleaning techniques. The concentration of Cu impurities on the wafer surface was monitored by TXRF (total reflection X-ray fluorescence) and XPS (X-ray photoelectron spectroscopy). Our results show that Cu impurities can be effectively removed by hydrogen plasma and UV/O3 cleaning techniques, if it is performed under optimum process conditions. The optimum process parameters for the remote hydrogen plasma cleaning are the rf power of 20 W and the exposure time of 5 min. The optimum exposure time of the UV/O3 cleaning for Cu impurity removal is 1 min. A two-step cleaning process composed of remote hydrogen plasma cleaning first and UV/O3 cleaning next has been found to be more effective than a single UV/O3 cleaning process, a single remote hydrogen plasma cleaning process, or a two-step cleaning process composed of UV/O3 cleaning first and remote hydrogen plasma cleaning next. Cleaning efficiency is maximized at optimum process conditions where Cu contaminant removal effect and recontamination effect are traded off. Increasing the process parameters higher than the optimum values would decrease the cleaning efficiency.
2024-07-03 20:16
국내논문
-
Powder Bed Fusion(PBF) 공정의 Laser rotation 적용 여부에 따른 17-4PH stainless steel 소재의 미세조직 및 기계적 특성 변화
17-4 precipitation hardened stainless steel (17-4PH SS) has been reported to have excellent mechanical properties and excellent corrosion resistance, and is one of the materials used and studied with the powder bed fusion (PBF) method. Powder bed fusion (PBF) is a new manufacturing technology that has recently attracted attention in automotive, aerospace and other industries because of its ability to produce complex geometries for high-strength and lightweight applications. In the PBF process, each layer has a different laser scan length resulting from the application of laser rotation. The laser rotation could affect the laser scan length, which causes a difference in the peak temperature and cooling rate of the deposited layer, resulting in microstructure changes. This work aims to investigate how varying the laser scan pattern in the PBF process affects the microstructure and mechanical properties of 17-4PH SS. A decrease in cooling rate was observed after applying laser scan rotation, resulting in a higher austenite phase fraction. It was confirmed that a transformation induced plasticity (TRIP) phenomenon affects mechanical characteristics. These results could be suggested for fabricating thin wall shaped such as tire blow mold parts in the powder bed fusion process using the 17-4PH SS.
2024-07-09 13:28
-
3D 프린팅 출력물을 위한 3D 모델링의 오류 분석과 해결방안
Digital technology has attempted to blur the boundaries between architectural design and fabrication, which have been established since the Renaissance. However, these boundaries still exist, due to the discontinuity between digital modeling and fabrication, which often derives from errors encountered in the process of file conversion. To bridge this discontinuity, this study intends to identify and analyze the causes of errors during the process of converting 3D modeling to Standard Triangulated Language (STL) file, and then to provide solutions that fix the errors. The STL file errors are results of failing to understand or ignoring the difference between 3D modeling for 3D printing and for visual presentation. For this reason, this study conducted an error analysis using Materialize Magics (STL editing and repairing software) to investigate types of the errors and to suggest ways of repairing 3D modeling with such errors.
2024-07-09 11:24
-
전기철도 전차선로 부품의 3차원 디지털화 연구
전기철도에서 전차선로는 팬터그래프의 입상량에 의한 기계적 진동과 이선 아크 등 전기적 피로가 누적되어 부품 간의 인터페이스 오류로 인한 장해가 발생할 수 있으므로, 사전에 이와 같은 문제를 판단하고 해소할 수 있는 기술이 요구되고 있다. 전차선로 용품은 제작 공차에 대한 신뢰성이 요구되고, 각 부품과의 연결성을 판단하고, 도면이 없는 전철부품에 대한 역설계 공정에 관한 연구는 필요하다. 따라서, 본 논문에서는 전차선로 시스템에서 디지털 기반의 부품관리체계 도입을 위한 용품의 3차원 데이터를 구현하였다. 디지털 데이터 제작을 위하여 전차선로 곡선당김금구에 적용하는 전차선용 회전클립을 3차원 스캐너를 이용하여 스캔하고, 이를 역설계하여 3차원 3D 데이터를 제작하였다. 또한, 부품의 조립성 분석을 위하여 제작한 데이터와 이를 이용하여 3D 프린터를 이용한 제작물을 상호 비교하여 상호 합치성을 확인하였다.
2024-07-09 11:23
-
급속 리뉴얼을 위한 전기철도 전철부품 제작 연구
전기철도의 전차선로는 다양한 부품의 조합으로 이루어져 있으며 차량 팬터그래프와의 접촉과 전기 에너지 전달을 위해 일정 이상의 기계적, 전기적 특성을 유지하여야 하며 이를 위해 금속제품을 주조방식으로 제조하고 있다. 전차선로는 속도에 따라 부품의 치수와 성능이 다르며 유지보수나 리뉴얼에 따라 부품 단종 시에 소량의 제작에도 주물을 제작하여야 하며 일부 제품은 규격이 없어 소품종 생산에 적합한 기술이 필요하다. 본 논문은 3D 프린팅을 이용한 클레비스형 단말클램프와 회전형 클립 제작을 위해 기존의 2차원 도면을 3D 각각 3차원 모델링을 수행하였다. 제작후 기계적 특성 시험결과 인장강도와 내력은 532 N/㎟와 189 N/㎟로 KRSA의 기준값인 600 N/㎟과 250 N/㎟에 비해 낮은 특성을 나타내었다. 재료의 화학적 특성 분석 결과 Ni가 다소 낮게 나타났으나 본 논문에서 제안한 3차원 모델링 기반의 전철부품 제작 기술은 설계, 제작 및 시공을 연계하거나 부품 보강을 통한 전차선로 특성향상기술에 활용될 것으로 기대된다.
2024-07-08 17:52
-
Selective compositional range exclusion via directed energy deposition to produce a defect-free Inconel 718S/ 316L functionally graded material
• A functionally graded material was fabricated with a compositional range of Inconel 718 and stainless steel 316L. • Defects were found in the 25 wt% Inconel 718/75 wt% stainless steel 316L region. • Various precipitates at the interfacial boundaries caused the defects. • Constitutional supercooling and columnar-to-equiaxial transition affected the formation of the defects. • The defective compositional range was removed to improve the mechanical reliability of the functionally graded material.
2024-07-08 11:42
-
철도 전철 부품의 스마트 제조기술 기초연구
Recently, smart manufacturing technology research is being conducted in various fields, using digital parts-based technologies. Components that are used for electrification in electric railways are manufactured using casting techniques. This is because the mechanical and electrical properties required to ensure safety considerably vary, and the standards defined for errors are strict. To apply digital parts-based manufacturing technology to parts for electrification, the design of existing parts must be 3D-modelled, and research must be conducted on manufacturing techniques using metals. In this study, we investigated digital laminate manufacturing technology for smart manufacturing of parts for electrification. The clevis-type terminal clamp of the contact wire was manufactured using stereolithography apparatus. The deviation, which was measured using a 3D hybrid scanner and a 3D coordinate measuring device, was observed to be approximately ± 500 μm. The model illustrated in this paper will be used as a reference to study metal train parts in the future. In addition, it is expected to be used as a pre-modelling development technology for manufacturing singular-shaped parts.
2024-07-08 11:39
-
Additive manufacturing of a shift block via laser powder bed fusion the simultaneous utilisation of optimised topology and a lattice structure
The precise shape of a shift block support for the turbine blade of a hovercraft was additively manufactured using 17–4 precipitation-hardened stainless steel (STS 630) powder through laser powder bed fusion (LPBF). Subsequently, heat treatment under the H900 condition increased the yield strength and fracture strain of the shift block to 1313 MPa and 11.5%, respectively, and enhanced its corrosion resistance to seawater. This improvement in mechanical and physical properties is primarily because Cu precipitates were uniformly distributed at the interfacial boundaries along with the simultaneous suppression of the formation of Cr23C6 precipitates with weak corrosion resistance. Furthermore, this was attributed to the phase transformation from the as-built STS 630 comprising a mixture of austenite, ferrite, and martensite to a dual mixture of ferrite and martensite after the heat treatment. Thereafter, we topologically optimised the shift block and adopted a lattice structure to apply the design for additive manufacturing (DfAM).
2024-07-08 11:37
-
UV/O3 와 ECR 플라즈마를 이용한 wafer storage box 로부터 발생하는 Si 웨이퍼 표면 위의 유기오염물 제거
The problem of organic contamination is still there due to the outgassing from the plastic materials in the storage boxes. Such organic contaminants have deleterious effects not only on the gate oxide integrity, but also on the chemical vapor deposition steps. In this paper, we report the experimental results for the removal of the organic contaminants existing on wafer surfaces by UV/O_3 cleaning, ECR H_2 plasma and ECR O_2 plasma cleaning. After cleaning, Si wafers were analyzed by Attenuated Total Reflection Fourier Transform Infrared Spectroscopy (ATR-FTIR) and Atomic Force Microscrope(AFM). The ECR oxygen plasma cleaning technique seems to be more effective than the ECR hydrogen plasma or the UV/O_3 cleaning technique for the removal of organic contaminants. Also, organic contaminants removal mechanisms of UV/O_3 cleaning, ECR H_2 plasma and ECR O_2 plasma cleaning are discussed.
2024-07-03 20:08
-
전해 크롬도금 대체용으로서의 CrC 스퍼터링에 관한 연구
Chromium carbide films were deposited on high speed steels using a Cr_3C_2$ target by magnetron sputtering. Effects of the deposition parameters (power, Ar pressure and substrate temperature) on deposition rates and surface roughnesses of the films were investigated. The morphologies of those films were characterized by scanning electron microscopy and atomic force microscopy. The grain size of the samples deposited using dc-power is larger than that using equivalent rf-power. The hardness of the sample increases with increasing rf-power, whereas the elastic modulus nearly does not change with rf-power. The optimum sputter deposition conditions for chromium carbide on high speed steels in the corrosion resistance aspect were found to be the rf-power with small roughness.
2024-07-03 19:14
-
Dry Cleaning for Organic Contaminants on Si wafer using UV/O~ 3 and ECR Plasma
2024-07-03 19:10
-
Removal of Cr and Zn impurities from the Si substrate using the remote plasma H2
In this communication, we report our experimental results on the removal of the organic contaminants existing on the surface of silicon wafers by a dry cleaning method using ECR plasma. After cleaning, Si wafers were characterized by Attenuated Total Reflection-Fourier Transform Infrared Spectroscopy (ATR-FTIR) and Atomic Force Microscropy (AFM). In ECR hydrogen plasma cleaning, the RMS surface roughness reduced significantly with increasing the exposure time but the removal of organic contaminants from tire silicon wafer was not very effective. In ECR oxygen plasma cleaning, the plasma exposure times to reach both the detection limit and the lowest RMS roughness were 40 and 10 sec, respectively and the optimum plasma exposure time is suggested to be 30 similar to 40 sec, considering both the effects of cleaning and surface roughening. Therefore, dry cleaning using ECR oxygen plasma seems to be more effective than that using ECR hydrogen plasma for the removal of organic contaminants.
2024-07-03 18:58
Research
우리 연구실의 연구정보를 안내합니다.
자세히 보기